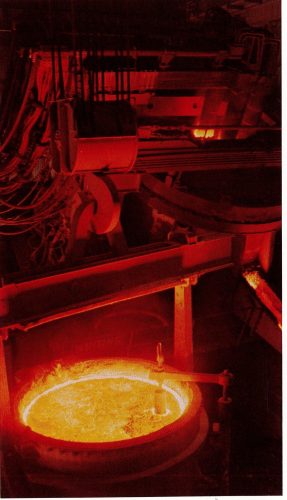
Ladle Holding 55-ton Heat
Whiting has developed ladles for virtually every holding and pouring requirement, including ladles for the steel and foundry industries. Ladles for molten metal (metal casting ladles) are subjected to extreme temperatures and heavy loads. Whiting produces ladles for foundry and ladle parts with lip pour, bottom tap, or outside teapot spouts. Made with welded or riveted construction, Whiting ladles used plain or anti-friction bearings, covered or open top. Whiting ladles are part of complete pouring systems.
With Whiting you can rest assured that replacement parts from worm shafts to gears are manufactured according to the original part drawing. Users are guaranteed the same high-quality component parts to ensure reliable operation and long service life, even in the most demanding industrial environments. All essential components of Whiting ladles are made of specialized materials that provide excellent wear resistance, sealing properties, and strength.
Worms are used to move the ladle’s tilting mechanism, which allows the ladle to pour its contents into another vessel or container. Whiting ladles use precision-cut worms that are designed to operate smoothly and reliably, even in high-temperature environments. These worms are often made of specialized materials, such as case-hardened steel or alloy steel, that provide excellent wear resistance and high strength.
Gears are another critical component of ladles, as they are responsible for transmitting power from the ladle’s motor to its rotating mechanism. Whiting ladles use precision-cut gears that are designed to operate quietly and reliably, even in high-temperature environments. These gears are often made of specialized materials, such as case-hardened steel or alloy steel, that provide excellent wear resistance and high strength.
Bearings and bushings are essential components of ladles, as they support the weight of the ladle and allow it to rotate smoothly. Whiting ladles use high-strength bearings and bushings that are designed to withstand the extreme temperatures and loads encountered in steel and foundry applications. These components are often made of specialized materials that provide excellent wear resistance and low friction.
Gaskets are used to seal the joints between the various components of the ladle, such as the lid and the body. Whiting ladles use high-quality gaskets that are designed to withstand the extreme temperatures and pressures encountered in steel and foundry applications. These gaskets are often made of specialized materials that provide excellent heat resistance and sealing properties.
Oil seals and plungers are used to maintain a constant oil pressure in the ladle’s hydraulic system, which is critical for its proper operation. Whiting ladles use high-quality oil seals and plungers that are designed to operate reliably and withstand the extreme temperatures and pressures encountered in steel and foundry applications. These components are often made of specialized materials, such as high-strength steel or heat-resistant rubber, that provide excellent wear resistance and sealing properties.